

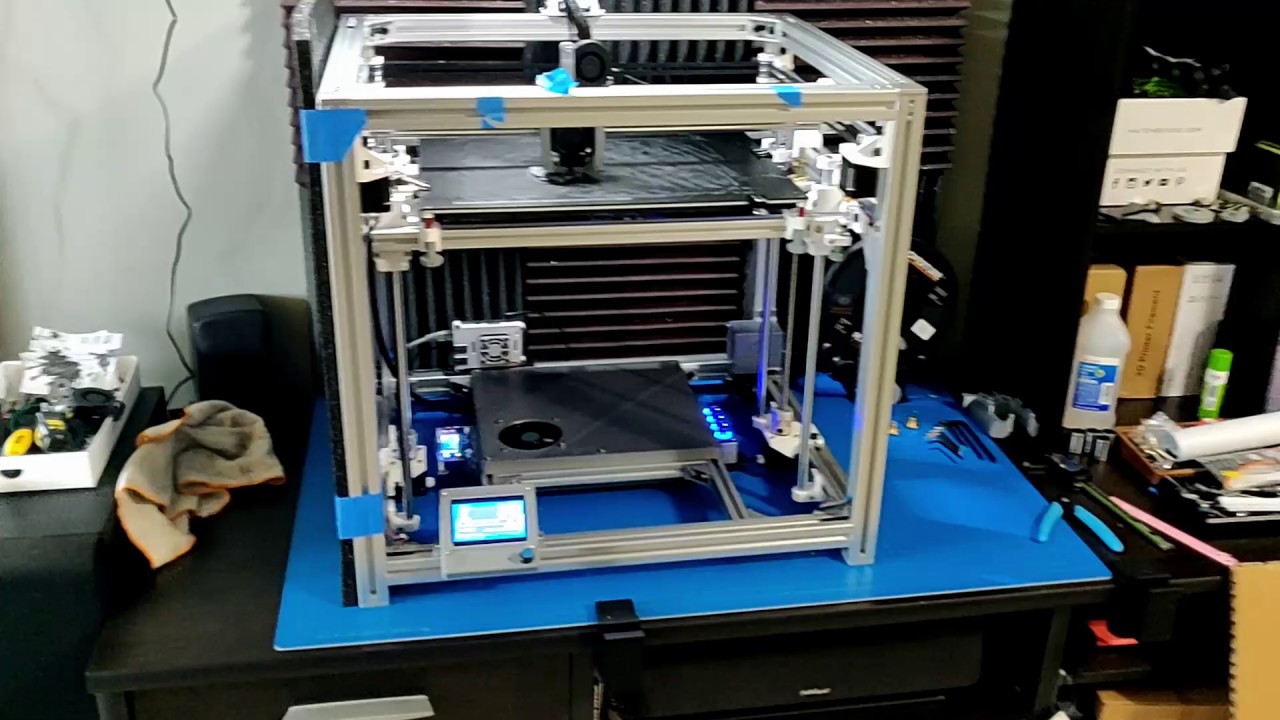
Facing the need to replace this, I instead decided to do an upgrade I’d planned a while ago. My plan had been to wait until the new printer is ready before doing any significant updates to the older printer. I haven’t started on the electronics yet. The parts are printed but I’m awaiting delivery of the non-printed parts. So far, I have the print bed mostly finished, but there’s a lot of work yet to do. Enter the Hypercube Evolution (HEVO): HEVO frame assembled Printer bed in place waiting on a silicon heaterĪs you can see, the current printer is still adequate for printing larger parts such as the ones used by the HEVO. I’ve finally bit the bullet and started working on a replacement. This is even more distressing knowing that I was able to print prototype versions perfectly when the printer was new, a feat I now find impossible to duplicate. I just can’t reliably print anything with fine detail, or even the Launch Escape System tower that is part of my Saturn IB and Saturn V rockets. I’ve tried replacing rods, bearings, slowing down, and any tips and tricks I’ve come across. Then I got a vibration problem that I’ve never been able to fix. Then the bed heater failed – upgrade number one. I was working on a project at the time that needed to progress so the result was me walking away from the printer for months at a time.Įventually I figured it out. I knew no one else with a 3D printer so I had no one to turn to for advice.

The primary cause was the nozzle being too close to the bed, and as a result it kept scraping the glue I used to help prints stick to the bed resulting in not just a jam but a clog. Out of the box it worked fine, but I struggled with jams. In particular, I had no idea about Z offsets and the effects it would have. I had many problems early due to my not having any experience.
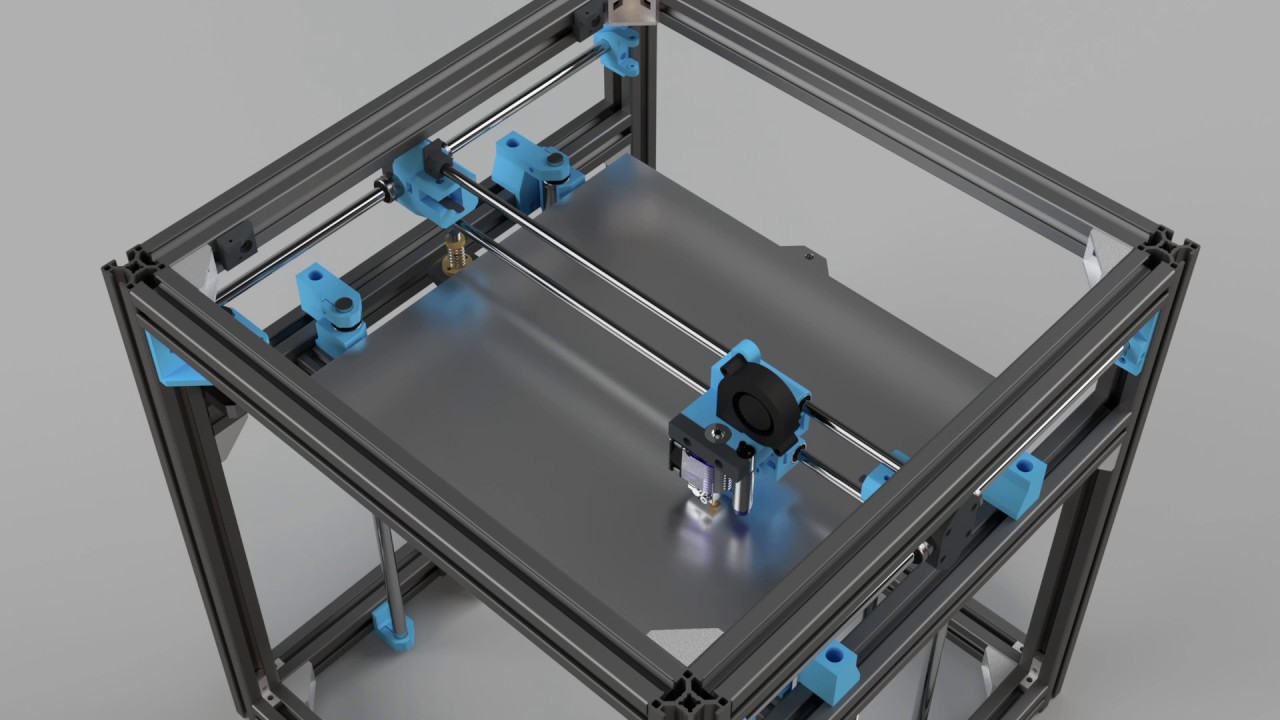
But, being the mechanical beasts that they are, that didn’t last. When I first got it, it was probably the best value for the money, and was giving great prints. I printed these parts at quite a high temp, 240 C with a low retraction rate to minimise delamination of layers when printing.If you’ve been following me for any length of time, you’ll know I’m not happy with my current 3D printer, a Robo 3D R1+. Printed with Amazon Basics Red PETG on an Ender Pro. I have uploaded a version which includes the stock X Flag allowance but I designed this primarily to work with my Compact Dual Duct assembly which has its own End stop\Flag arrangement. The part also uses M3 Nylocs for bolt retention except for 3 x M3 thermal inserts for the X & Y flags. I have also set the last 15 mm of the print to 100% in my slicer( I am aware this may be a bit of an overkill but it only added a small amount of print time relative to such a long print). This part is still printed in the original print orientation but I have included 4 x M3 x 50mm bolts which retain the parts forward of the idler shafts to help reduce splitting. This part equally may have some long term issues but to date appears to be more robust than my previous printed parts. I have since tried several remix but the ones I tried still had issue albeit not the ones the stock parts demonstrated. My stock XY Joiners on my Hypercube Evo build started to split under the tension of the drive belts and the general print orientation. I have included step files for the parts if you require to create a 8mm to 8mm derivative.
